Table of Contents
customized badges
The production process of custom badges:In today’s era of personalization, customized badges have become a popular choice for many occasions with their unique charm and rich expressiveness. Whether it is corporate promotion, event commemoration, or personal collection, customized badges can show unique value. So, how is a beautiful customized badge made? Let’s take a deep look at the customized badge production process.

Demand communication
The first step in customizing a badge is to communicate with customers about the needs. At this stage, the badge manufacturer will discuss with customers in detail about the purpose, design requirements, quantity, budget, and other aspects of the badge.
Keywords: customized badge, demand communication, badge production
For example, if it is a corporate customized badge, you may need to consider the company’s logo, slogan, values and other elements on the badge to achieve the purpose of promoting the corporate brand. If it is an event commemorative badge, it may be necessary to design it in combination with the theme, time, location and other factors of the event. Through sufficient demand communication, the manufacturer can better understand the customer’s needs and provide a clear direction for subsequent design and production.
Design plan
After understanding the customer’s needs, the designer of the badge manufacturer will begin to develop a design plan. The design plan usually includes the shape, size, color, pattern and other aspects of the badge.
Keywords: design plan, badge making, custom badge
Designers will use professional design software to make creative designs according to customer requirements. During the design process, designers will focus on the beauty, practicality and uniqueness of the badge. At the same time, designers will also consider the production process and cost of the badge to ensure that the design plan can not only meet customer needs but also be feasible. After the design plan is completed, it will be submitted to the customer for review and confirmation. Customers can make modifications, and designers will make adjustments based on customer feedback until the customer is satisfied.
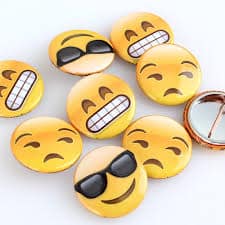
Material selection
The material selection of custom badges is very important. Different materials will affect the quality, appearance and price of badges. Common badge making materials include copper, iron, zinc alloy, stainless steel, etc.
Keywords: material selection, badge making, custom badges
Copper badges have the advantages of good texture, bright color, and corrosion resistance, which are suitable for making high-end badges. Iron badges have low cost, but are easy to rust and need surface treatment. Zinc alloy badges have the characteristics of high strength, good plasticity, and smooth surface.
They are currently the most commonly used badge making materials. Stainless steel badges have the advantages of corrosion resistance, high temperature resistance, and not easy to deform, which are suitable for making badges for outdoor use. In addition to metal materials, some non-metallic materials such as acrylic and plastic can also be used to make badges. When choosing materials, it is necessary to comprehensively consider factors such as the purpose of the badge, design requirements and budget.
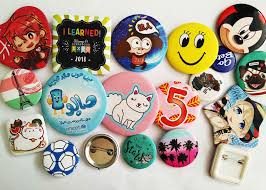
Mold making
Mold making is a key link in the process of custom badges making. The quality of the mold directly affects the accuracy and quality of the badge.
Keywords: mold making, badge making, custom badges
First, the designer will make a drawing of the mold according to the design plan. Then, the mold master will use professional equipment and tools to make the mold according to the drawing. Mold making usually uses processes such as engraving and electric spark, which requires very high precision and technical level. After the mold is made, strict inspection and debugging are required to ensure that the size and shape of the mold meet the requirements.
Die casting or stamping
For metal badges, die casting or stamping is a common manufacturing process. Die casting is to inject molten metal into the mold and form it by high pressure. Stamping is to use a punch press to punch the metal sheet into the shape of a badge.
Keywords: die-casting, stamping, badge making, custom badges
The die-casting process is suitable for making badges with complex shapes and high precision requirements. The stamping process is suitable for making badges with large quantities and simple shapes. During the die-casting or stamping process, it is necessary to control parameters such as temperature and pressure to ensure the quality and precision of the badge. At the same time, the badge needs to be deburred, polished, etc. to make its surface smooth and flat.
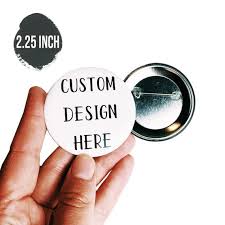
Surface treatment
After the badge is made, it is also necessary to perform surface treatment to improve the beauty and durability of the badge. Common surface treatment processes include electroplating, baking paint, and dripping glue.
Keywords: surface treatment, badge making, custom badges
Electroplating is to plate a layer of metal on the surface of the badge, such as gold, silver, copper, etc., to give it a metallic luster and anti-corrosion performance. Baking paint is to apply a layer of paint on the surface of the badge, and then bake it at high temperature to make it bright in color and not easy to fade. Glue dripping is to apply a layer of transparent glue on the surface of the badge to make it three-dimensional and waterproof. Different surface treatment processes can be selected according to customer needs and design requirements.
Printing or Etching
If the badge needs to have text, patterns and other contents, it can be made by printing or etching. Printing is to print ink on the surface of the badge, which is suitable for making badges with rich colors and complex patterns. Etching is to carve text, patterns and other contents on the surface of the badge by chemical corrosion, which is suitable for making fine badges.
Keywords: printing, etching, badge making, custom badges
During the printing or etching process, attention should be paid to the quality of the ink, the accuracy of printing and the depth of etching to ensure the quality and effect of the badge.
Quality Inspection
Strict quality inspection is required in every link of badge making to ensure that the quality of the badge meets the requirements. Quality inspection includes appearance inspection, size inspection, hardness inspection and other aspects.
Keywords: quality inspection, badge making, custom badges
Appearance inspection mainly checks whether the surface of the badge is smooth, whether there are scratches, whether the color is uniform, etc. Size inspection is to check whether the size of the badge meets the design requirements. Hardness inspection is to check whether the hardness of the badge meets the standard. Only through strict quality inspection can the quality and quality of the badge be guaranteed.
Packaging and delivery
Finally, the finished badge will be packaged and shipped. Packaging usually uses paper boxes, plastic bags and other materials to ensure that the badge is not damaged during transportation.
Keywords: packaging and delivery, badge production, custom badge
Before delivery, the manufacturer will confirm the delivery address and contact information with the customer to ensure that the badge can be delivered to the customer accurately.
In short, the custom badges production process is a complex and delicate process, which requires demand communication, design plan, material selection, mold making, die casting or stamping, surface treatment, printing or etching, quality inspection, packaging and delivery. Each link requires professional technology and strict quality control to produce exquisite custom badges. I hope that through the introduction of this article, you can have a deeper understanding of the custom badges production process and provide a reference for everyone when choosing custom badges.
Click here for more information about wristbands: https://www.topwristband.com
Reference Website:https://www.newyorkcityfc.com/news/new-york-city-fc-unveil-updated-club-badge